Finishing textiles with ultrasound and conserving resources
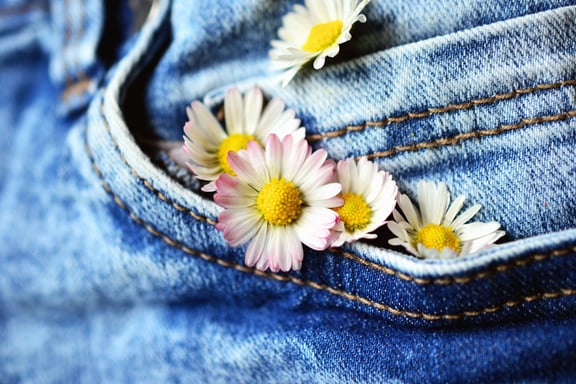
In addition, conventional textile finishing plants, especially in the countries with the largest production volumes (China and India), often have a very long service life and are therefore not up to date with the latest technology.
Based on our more than 20 years of experience in the field of industrial parts cleaning and this deep know-how we developed a solution which uses the phenomenon of acoustic cavitation especially for cleaning and finishing of textiles.
Solution
The SonoPower Textile System is suitable for the wet-chemical treatment of stretched web materials such as knitted fabrics, woven fabrics, nonwovens and laminates of any width inline in the finishing process. Materials made of cotton, synthetics, blended fabrics, elastic fabrics or nonwovens can be treated.
The system can also be retrofitted into existing textile finishing lines. The oscillating system is installed in a tank, which usually already exists on the plant side, and is operated via an ultrasonic generator. When the ultrasound is activated, the generator supplies the ultrasonic transducer with electrical energy. The transducer converts the electrical energy into sound waves, which are emitted into the liquid as mechanical energy.
The unrivaled homogenous, streak-free and reproducible result is ensured by the patent-pending technical design and layout of the plate transducer. Particularly when finishing the increasingly common fabrics with elastic content, SonoPower Textile significantly reduces waste.
In brief:
- 30 % water savings
- 30 % less textile auxiliaries (chemicals)
- 50 % less energy consumption
- 50 % less CO2-emissions
- Shorter throughput times
- Reduction of plant length by up to 60 %
- Easy subsequent integration into existing plants
- Treatment inline in the finishing process
Back to Blog page