Textiles that protect their users – and help the environment
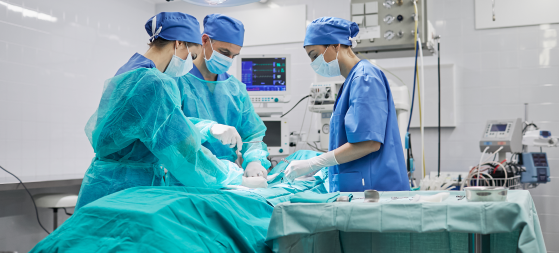
Innovative ultrasonic process for antimicrobial textile finishing
The outbreak of pandemics such as the current corona pandemic and the worldwide increasing number of hospital-acquired infections with multi- resistant bacteria generate an increasing need for effective protection measures - in the fields of healthcare and politics as well as in the society. These preventive strategies include, among other things, textiles with antimicrobial and antiviral finishes – assuming these finishes offer durable and reliable protection. The development of a Sono Finishing process at Bar Ilan University in Israel was a flagship project in this regard. This novel process makes it possible to add highly effective antibacterial, antiviral, and fungicidal properties to textiles of any kind both durably and sustainably using ultrasound. "The impregnation must be capable of withstanding the kind of high-temperature washing cycles typically employed in the medical sector and must not lose any of its effectiveness," comments Liat Goldhammer, Chief Technology Officer (CTO) at Sonovia Ltd., describing a key requirement.
From the laboratory to mass production
The Israeli start-up began to transfer the patented process from a small university lab-based operation to production technology for industrial mass production in 2017. To this end, the young company entered into a strategic partnership with Brueckner Textile Technologies and Weber Ultrasonics AG. The Karlsbad-based manufacturer of ultrasonic systems for applications including cleaning, welding, and cutting developed a specific series production-ready ultrasonic solution for this application. This meets current requirements in the textile industry in terms of productivity, process reliability, and cost efficiency. It also ensures that the active ingredient formulation with zinc oxide nanoparticles is incorporated optimally into the respective material in the single-step sonochemical process. This is based on the physical phenomenon of acoustic cavitation, whereby small bubbles form in the liquid mixed with the antimicrobial formulation. These grow and then collapse, thereby generating shock waves. The effect leads to strong currents, which in turn permanently anchor the nanoparticles on the textile surface. "This is a key feature that sets our technology apart from classic textile finishing processes, which work with chemical binders," explains Liat Goldhammer. Since these chemical components are progressively rinsed out with each washing cycle, not only does the protective function of the impregnation start to fade, it also leads to a considerable environmental burden.
Proven effectiveness against bacteria and viruses
The antibacterial properties and their durability have long since been demonstrated in testing. A small study on a burns ward at a Bulgarian hospital also underlined the effectiveness – including for bacteria that are resistant to antibiotics. Sonovia’s production of Sono Masks, which are being produced from fabrics treated using the process, have also already been tested and proven successful against a virus that resembles the Sars-CoV-2 coronavirus. The company is currently awaiting the results of testing with the new CoV 19 coronavirus and has begun the Sono Masks CE and FDA accredition. The fabrics have also been demonstrated to retain their full antimicrobial properties even after 90 washes at 60 °C
Back to Blog page