Inseparable connections with ultrasound in photovoltaics
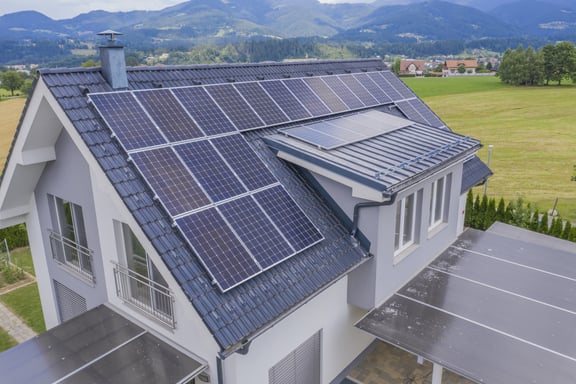
Maximum yield through power optimizers
The manufacture of solar modules and junction boxes is subject to high demands in terms of durability and hermetics. Ultrasonic welding is an indispensable process here. It ensures absolutely leak-proof products with high production speed and low energy consumption.
The use of solar energy is an environmentally friendly and renewable energy source, especially for property owners, to cover the increasing demand for electrical energy due to e-mobility, air conditioning and heating in a cost-effective and sustainable manner. However, not all roof surfaces are 100% suitable for equipping with solar modules, as shade from trees or other parts of the building, such as dormers, falls on the modules during the course of the day. These areas are often not fitted with modules in the first place or, if fitted, these modules are deactivated when shaded, which leads to reduced power yield and hotspots on the remaining active solar modules.
BRC Solar, founded in Ettlingen in 2018, closes this gap with the development and production of power optimizers for solar modules, especially under conditions where shade, different orientations or different module inclinations impair efficiency.
The power optimizers can be used with all common inverters, making them extremely flexible and adaptable for different solar systems. They are characterized by durable electronics thanks to GaN technology, a true stand-by function to minimize energy losses and easy installation without special tools or required training
Rain or shine
The requirements for the power optimizers, which generally have to withstand wind and weather when exposed on building roofs, are absolute tightness and weather resistance. The intelligent electronics in the housing must be strain-relieved from the connected supply lines to the solar modules and protected from moisture. To achieve this, the strain relief and the housing are welded using ultrasonic technology. “We offer a 25-year guarantee on our power optimizers, which are permanently exposed to the weather. We play it safe and use ultrasonic welding, an established and proven process in the photovoltaic industry for sealing junction boxes,” says company founder Timm Czarnecki.
Absolutely tight and protected thanks to ultrasonic technology
In ultrasonic welding, high-frequency mechanical vibrations generate frictional heat by exciting the molecular chains in the plastics. This causes the component to melt in the joining zone. The parts to be joined are then permanently welded together under a defined contact pressure. The process enables a fast, precise and, above all, reliable connection and does not require any additives such as adhesives.
The strain relief is welded to the housing quickly and energy-efficiently using 35 kHz systems from Weber Ultrasonics' Saphir line. BRC Solar uses a fully automated production line with an output of several hundred products per shift. In addition, a manual ultrasonic welding unit is available in the development department for testing and optimization. Both systems are controlled via a touch control unit with comprehensive, intuitive software and offer full control over all important functions at all times. The relevant welding parameters such as distance, time, energy and power are permanently monitored by means of set quality windows. Deviations from the target parameters are displayed to the worker by the system. The process parameters resulting from the welding process can also be documented and archived for quality assurance purposes.
A visual representation of the welding process makes it easier to determine the optimum process parameters.
“We are very satisfied with our collaboration with Weber Ultrasonics. The service, price and technical support are just right. Speed in finding solutions is a key factor in our industry. The ability to carry out tests and trials in the Application Center with the experienced ultrasonic experts, even at short notice, is a great help to us in product development,” adds Czarnecki. A further system for a performance optimizer with monitoring functions is already being planned.
Learn more & Saphir System:
https://www.weber-ultrasonics.com/en/saphir-system
Back to Blog page