Recycling batteries more efficiently
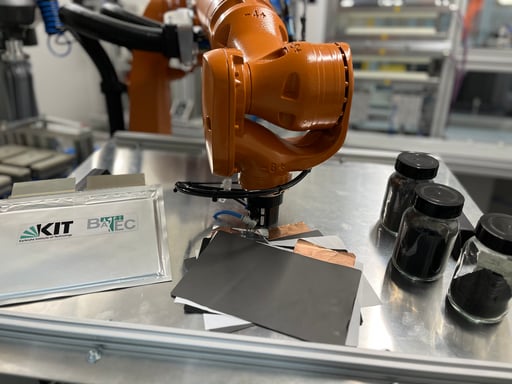
The market for electric cars is growing rapidly and with it the demand for lithium-ion batteries. Recycling them is an important part of the production cycle. Current processes break down the active battery materials back into their molecular components - but with high energy and chemical input. In a large-scale joint project, researchers from the Karlsruhe Institute of Technology (KIT) and partners from industrial companies are therefore developing a complete process chain to recycle used batteries more efficiently by recovering the active components while maintaining their function.
Recycling used lithium-ion batteries in a sustainable and closed material cycle
Such a process chain for direct recycling has not yet become established in the industry. The material behavior of the recovered recyclate cannot be predicted either. In addition, there are no criteria and rules for evaluating the recyclability of the aged material and there is currently a lack of practicable, economical solutions for breaking down the various battery packs into their individual components without great effort. "Our joint project addresses these critical points and is primarily concerned with the development of an agile process chain for the direct recycling of lithium-ion batteries and the regeneration of the active materials recovered in this way," says project coordinator Dr. Thomas Dreyer from Weber Ultrasonics. It is also important that the process is variably tailored to different starting materials for battery production as well as for production rejects and can process different battery formats and designs. "The aim is also to replace the energy-intensive process steps of the recycling methods currently in use and to supply sustainably recycled, high-quality secondary materials in the sense of a circular economy," says scientific coordinator Dr. Marco Gleiß.
Joint project launched
The Federal Ministry of Education and Research is funding the three-year project with almost three million euros. The project consortium, led by Weber Ultrasonics AG, consists of ten partners and one associated partner. It comprises four KIT institutes - wbk Institute of Production Engineering, Institute of Mechanical Process Engineering and Mechanics, Institute of Applied Geosciences - Chair of Geochemistry & Deposit Science and the Thin Film Technology working group - as well as six industrial partners: the battery cell manufacturer PowerCo SE, the materials technology and recycling group Umicore AG & Co. KG, the experts for gripping and handling technology SCHUNK SE & Co. KG, the company FIBRO LÄPPLE TECHNOLOGY GMBH as plant integrator and the plant manufacturers Carl Padberg Zentrifugenbau GmbH and Weber Ultrasonics AG. In addition, Siemens is supporting the project from a control and digitalization perspective as part of an associated partnership.
*Photo: KIT
Back to Blog page